Webなんでも鋳物館 鋳物ができるまで
鋳物は、砂を固めて作った鋳型に、溶けた鉄(鋳鉄)を流し込み、凝固、冷却して作られます。現代では、これを高い生産性で作るため、高速自動造型ラインが一般的になっています。それでは、この現代の鋳物製造ラインの各工程をご紹介しましょう。
※各工程図はアニメーションになっています。読み込みに時間がかかる場合がありますが、アニメが動き出すまでもうしばらくお待ち下さい。
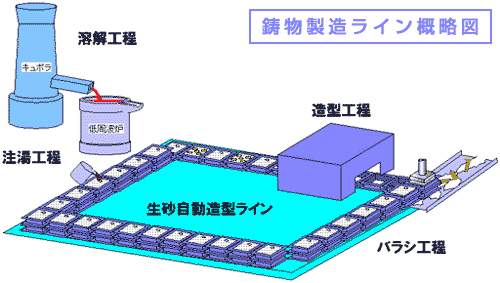
-
溶解
「キュポラ」と呼ばれる筒状の炉で溶解を行います。上部から、材料(銑鉄、鋼屑、戻し材)と燃料(コークス)を層状に入れます。下部側面から熱風を送って、コークスを燃焼させ、炉内温度を1600℃以上にすることで、鋳鉄を溶解します。
材料と燃料は、順次下に落ちながら、下部の出湯口から連続的に溶けた鋳鉄が流れ出します。(上部の材料は、炉内を通り抜ける熱風で予熱されるため、キュポラは熱効率が高い溶解炉です。
溶解炉としては、キュポラの他に、電気誘導炉が用いられることもあります。)※戻し材…後工程からリサイクルされる鋳物の端材
-
造型
数%の水とベントナイト(粘土)を加えて混練した砂を鋳枠の中に投入し、スクイズ(押し固め)して製品模型から転写型(=鋳型と呼ぶ)をとります。 鋳型の砂づまりを均一にすることで鋳物の寸法精度が向上します。 水と粘土を加えた生砂鋳型の他に樹脂を混ぜた硬化型も用いられています。
-
注湯
「トリベ」と呼ばれる、溶湯専用の入れ物から、溶湯を鋳型の注湯口に注ぎます。
注湯は、「素早くかつ静かに」が原則です。最近では、機械的に注湯を行う自動注湯機が一般的ですが、手動の場合は、トリベを操作する作業者の熟練度が要求されます。
製品の中の中空部分を形成するために、「中子(なかご)」と呼ばれる補助鋳型が入れられています。 -
バラシ
砂型の中で必要な時間をかけて冷やされた鋳物は、金枠から砂ごと分離されます。この時、砂は崩壊し、元の砂粒となって回収再生されます。鋳物は表面に残った砂をきれいに落としてから、製品となる部分と、型内へ溶湯を流入させるための経路として使われた、「方案」と呼ばれる部分に分離します。方案部分は溶かして再利用され、製品部分は機械加工等を施し、組立て工程へ送られます。